UK laundry stores use RFID technology to manage washed items
- Share
- Issue Time
- Apr 19,2023
Summary
The commercial laundry and textile rental company, has used RFID readers to read labels attached to linen, bags, and anti-roll labels used to transport linen products provided to customers at the "Super Laundry". By using the RFID system, the washing company can not only better manage linen inventory, but also share this information with customers.
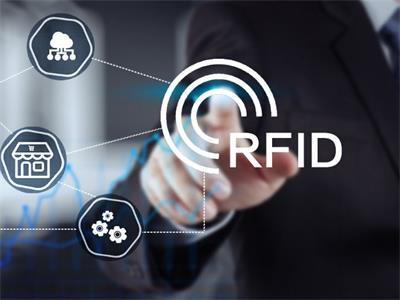
Fisher Services, a commercial laundry and textile rental company, has used RFID readers to read labels attached to linen, all bags, and anti-roll labels used to transport linen products provided to customers at the "Super Laundry" in Glasgow. This allows the company to understand the time when items are received, washed, and delivered to customers. By using the RFID system, the washing company can not only better manage linen inventory, but also share this information with customers.
Since 1900, Fisher has been providing work clothes and linen laundry services in Scotland. Now, the company is renting its own linen products from hotels and restaurants, such as bed sheets, bedding, and towels; Customers can clean, dry, fold, or return at the nearby Fisher laundry.
Fisher Services states that the company has been growing. The company can wash/iron every two weeks and deliver over 2 million items. In March 2016, the company opened a "Super Laundry" in Glasgow. Michael Jones, the company's management manager, stated that the company provides services to a total of 2000 hotels, while the new store in Glasgow serves 300 customers within a 50-mile radius.
Due to its huge business volume, Fisher has encountered some loss of items that cannot be attributed to a certain level of responsibility. The company's annual revenue is approximately $52.7 million, with annual losses resulting in expenses of up to $1.5 million. So, Fishers began to seek solutions to simplify the entry and exit of items into washing facilities, and to identify the time and location of lost items.
Munier said, "Customers can view real-time information on returned linen products through a web interface. Our system has been developed for 8 years and has been in use in 300 locations, including the washing market, logistics, tool management, and planning areas.
Jones stated that the goal of the system is to better understand the location of linen products. If the technology runs well, he hopes to install this system in some of the clients' hotels or assign handheld readers to users to increase visibility.
In the coming years, Fisher will install this RFID technology in at least four washing shops.