RFID Solution for epidemic prevention material management system
- Share
- Issue Time
- Mar 1,2023
Summary
RFID epidemic prevention material management system is an information, intelligent and standardized system that relies on mutual 3D technology, cloud computing, big data, RFID technology, database technology, AI and video analysis technology to manage and analyze epidemic prevention materials uniformly.
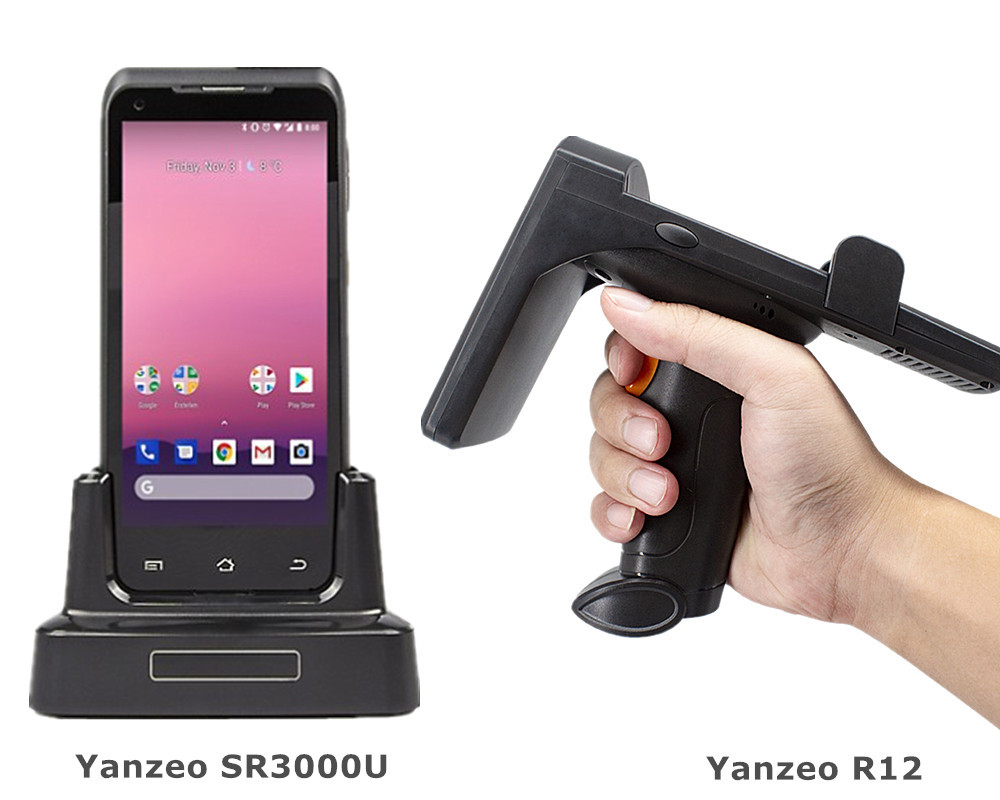
System overview
RFID epidemic prevention material management system is an information, intelligent and standardized system that relies on mutual 3D technology, cloud computing, big data, RFID technology, database technology, AI and video analysis technology to manage and analyze epidemic prevention materials uniformly.
With the sudden outbreak of the epidemic, the supply of living materials across the country is in short supply. On the basis of solidarity and mutual assistance of all countries, the quantity of emergency materials is huge, and it is inevitable to be negligent only to rely on manual management, including the warehousing, statistics, management, etc. of emergency materials. Only relying on human resources to manage is just a piece of paper. Then, in combination with the difficulties and needs of emergency materials, the epidemic prevention materials management system would be much practical.
Background and significance
By using RFID technology, we can manage the import and export of epidemic prevention materials, improve efficiency and provide the accuracy of system data. The main objectives are as follows:
Reduce human operation leakage, improve management level and reduce potential safety hazards;
Real-time data collection and consistency of items and records;
Reliable and stable data collection and accurate data;
The report forms are sorted and summarized manually change to be completed by computer;
Improve the efficiency of data management, timely register the detailed accounts of all kinds of safety materials to achieve the consistency of accounts, accounts and materials, and accounts and cards;
The system is flexible and has expansion function;
The system is practical and easy to operate, aiming at users with different levels of professional quality.
System application
The system application is divided into three logical steps: acquisition layer, application layer and presentation layer.
Acquisition: Readers (desktop readers, fixed readers, etc.) read the electronic tag data, and then transmit it to the RFID middleware system through the network.
Application: build materials management, maintenance, query and other applications based on RFID middleware system.
Display: users can log in to the system through ERP system, computer, handheld, display screen, etc.
Application value
The epidemic prevention material management system is mainly developed according to the characteristics of emergency material business management, focusing on the management of the acceptance and warehousing of epidemic prevention emergency materials, material distribution, valuable material positioning, material allocation status tracking and other links, and evaluating from multiple perspectives to create value for customers.
Timely feedback on supplier supply quality
Track the source of materials, reflect the quality of the goods supplied by the supplier in time, and facilitate the warehouse keeper to understand the quality of the goods supplied by the supplier in time, and replace or repair the equipment in time.
Life cycle management of emergency materials
The establishment of the system has strengthened the management of information related to flood control materials, and can timely grasp the reserve situation and types of flood control and drought relief materials, and strictly manage the supply, reserve, allocation and use of materials.
Strict control to ensure consistency between account and reality
Automatic collection of goods in and out of warehouse can improve work efficiency and reduce the probability of errors in the operation of goods in and out of warehouse. Management personnel can understand the current inventory of emergency materials in real time, provide decision-making basis for dispatching and rescue, and timely supplement emergency materials.
Intelligent handheld terminal application to improve work efficiency and reduce errors
RFID handset breaks the traditional warehouse management mode and combines barcode or RFID label to identify goods more accurately and efficiently, reducing management errors caused by human factors.
Application of cargo area positioning technology to quickly locate goods
Through the use of active RFID positioning tags, the system can quickly locate the storage location of goods and display them graphically.
Material warning reminder
If some epidemic prevention materials have a shelf life or need regular maintenance or due treatment, the shelf life is registered when the materials are warehoused. If the goods are still in the warehouse after the shelf life, remind the storekeeper or the police officer. Unauthorized outbound alarm, displacement change alarm, smoke alarm, etc.