Application Management of RFID Technology in Furniture Supply Chain
- Share
- Issue Time
- Apr 2,2022
Summary
RFID can achieve these needs. It has become an analytical tool for inventory management and provides inventory visibility. This service can help companies improve inventory accuracy, reduce the risk of out-of-stock, conduct omni-channel sales, and improve customer experience. and prevent theft of goods.The drawbacks of using labels and manual scanning are exposed, with deficiencies in productivity, accuracy, and inventory visibility.
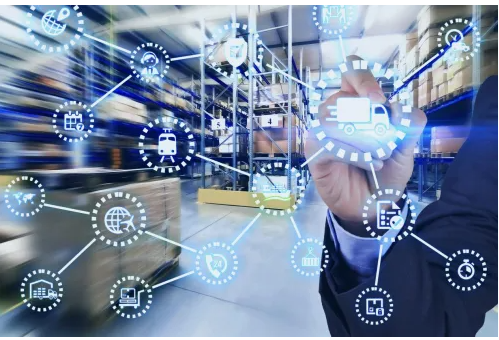
- The supply chain involves the entire process of product selection from raw material procurement, production and processing, warehousing, transportation, distribution, to sales.
- The production characteristics of furniture enterprises are that the production cycle is long, the product structure is complex, the process route and equipment configuration are abundant and often flexible, the phenomenon of temporary order insertion is many, and the types of parts and components are various. Automation is mainly used at the unit level. The use of radio frequency identification technology to attach radio frequency identification tags to furniture parts keeps the furniture in a state of information monitoring before it is sold, and makes the information more transparent in front of consumers, which is also conducive to improving supply. Specifically, RlFD technology can be applied to the following management of furniture supply chain:
- (1) Raw material procurement
- In the traditional production method, the porcelain transfer of various materials used for furniture production in each production process cannot be recorded in detail. We can set a label for each type of product, and carry out initial data information for the entire process of the product. Input, such as tree species, growth time and other information, the performance label is attached to the corresponding wood like an ID card, which can provide detailed information for the furniture supply chain, and provide source data for product traceability, so as to trace whether the furniture is in the growth process. There is a record of whether there are pests and diseases, whether the wood is produced and processed with poor quality or excessive medication, and even the production and harvest time of the wood are well recorded.
- (2) Manufacturing link
- Putting RFID tags on furniture parts on the production line is like setting up an ID card for the furniture, which can quickly track the position on the entire production line. After storing the information in digital storage, all parts batch numbers can be generated and matched. Online query display and input of management, production process, plan, status, equipment phase analysis and other information, thus discarding the links that must be manually adjusted through paper documents, realizing paperless operation, improving automation and making managers Understand the production progress of each process, reasonably balance the production line, and finally maximize the production capacity of the production line.
- (3) Warehousing and transportation links
- In the process of warehousing and transportation, most furniture enterprises mainly rely on manual points for entering and leaving the warehouse, which is inefficient and prone to errors. In the process of entering and leaving the warehouse, in order to save time, deliverymen and warehouse administrators avoid frequently changing the product name, model, color, quantity, etc. The key information is abbreviated, causing the information to be inaccurate, and the application of RFID technology can effectively avoid these situations. The products are transported to the warehouse logistics center of the distributor through the transportation department, and the staff will pass the RFID reading equipment installed at the entrance of the warehouse. , read and receive the electrical label information on the product, and match it with the information of the shipper, if it is consistent, proceed to the next step of warehousing and putting on the shelf. If the product information does not match the AsN information of the shipper during the warehousing process, manual intervention is performed.
- (4) Sales link
- In the process of sales and purchase, in addition to selling the product to realize short-term value, it is also necessary to analyze the consumer demand, and then guide the product design.
- (5) Inventory visibility link
- For supply chain managers, the application of RFID has gone far beyond warehouse management and simple positioning functions, and its main application is to achieve inventory visibility.
- We need to master the entire inventory of goods from manufacturing to sales, and manufacturing plants need to know where the raw materials are and when they can arrive at the factory. Analyzing the quantity of work in process can help us analyze the bottleneck problem in the system.
- Online and offline stores need to know real-time inventory of finished SKUs, which is a must for e-commerce and retail businesses.
- RFID can achieve these needs. It has become a management analysis tool and provides inventory visibility. This service can help companies improve management accuracy, reduce the risk of out-of-stock, conduct omni-channel sales, improve customer experience and Prevent goods from being stolen.
- The drawbacks of using labels and manual scanning are exposed, with deficiencies in productivity, accuracy, and inventory visibility.